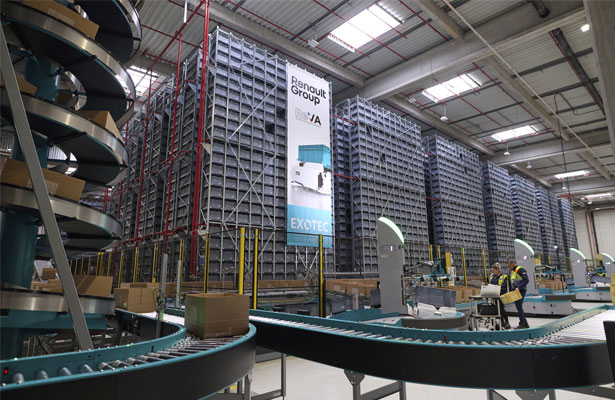
Renault’s New Automated Supply Chain Breaks New Ground
Renault Group has unveiled a groundbreaking fully automated logistics facility at its Villeroy site, setting a new benchmark in automotive supply chain management. This initiative, launched in 2024, shows Renault’s commitment to innovation, efficiency and customer satisfaction.
At the core of this automation revolution is the ReVA (Renault Villeroy Automatisation) project, which integrates 191 highly skilled warehouse robots. These advanced machines manage the entire flow of parts from receipt to shipment!
The impact of this automation has been remarkable. After a ramp-up phase in January, the ReVA logistics solution can now process up to 4,000 order lines per hour at peak times. On June 19, it celebrated a significant milestone by delivering its millionth order line. The system has reduced order processing time from two hours to just 20 minutes – a sixfold improvement.
This dramatic increase in efficiency has allowed Renault to boost its overall daily parts output by 25% while still growing its workforce. The facility now handles up to 40,000 order lines daily, managing 110,000 references, including 20,000 through the new logistics tool.
Enhancing Working Conditions And Safety
The automation has significantly improved working conditions for warehouse employees. It has virtually eliminated the need for long-distance walking to perform tasks such as picking, replenishing, and checking inventory.
All tasks are now performed at ergonomic heights, with parts ‘delivered’ to operators without the risk of injury. This “goods to person” (GTP) system represents a paradigm shift in warehouse operations.
Driving Sustainability
The new warehouse robots have cut the site’s energy consumption by 30% compared to traditional handling equipment. Additionally, the use of 65,000 recycled plastic bins for parts storage contributes to Renault’s objective of reducing its impact on natural resources.
These initiatives align with Renault’s broader goal of achieving carbon neutrality by 2040.

Renault’s New Automated Supply Chain Breaks New Ground
Elevating Customer Satisfaction
By centralising over 80% of its French operations in the Villeroy warehouse, Renault has significantly reduced order processing times and guaranteed faster deliveries. Parts ordered by 5.30 pm are now dispatched for delivery by 8 am the following morning.
This speed and precision in order management have optimised customer service rates and increased overall satisfaction levels.
The Villeroy facility manages parts for both Renault’s latest models (like Scenic and Rafale) and older vehicles, ensuring comprehensive after-sales support. This versatility allows Renault to tackle all types of customer maintenance or repair solutions with the highest level of service.
The Future Of Automotive Logistics
Xavier Lhors, Director of After-Sales Logistics at Renault Group, emphasises the strategic importance of this initiative: “By working with our logistics partners and equipping our supply chain with advanced robotics, we are positioning our after-sales logistics, and our Villeroy site in particular, at the cutting edge of innovation. This solution strengthens our commitment to customer satisfaction, which remains a priority for all of us.”
As Renault pioneers this fully automated approach, it sets a new standard for the automotive industry. The success of the Villeroy facility may well inspire similar transformations across the sector, potentially reshaping the landscape of automotive logistics and after-sales service.
By embracing cutting-edge automation, Renault is not just optimising its operations – it’s redefining what’s possible in automotive supply chain management. As the industry watches closely, Renault’s bold move may mark the beginning of a new era in smart, efficient, and customer-focused automotive logistics.